Laser or plasma technology
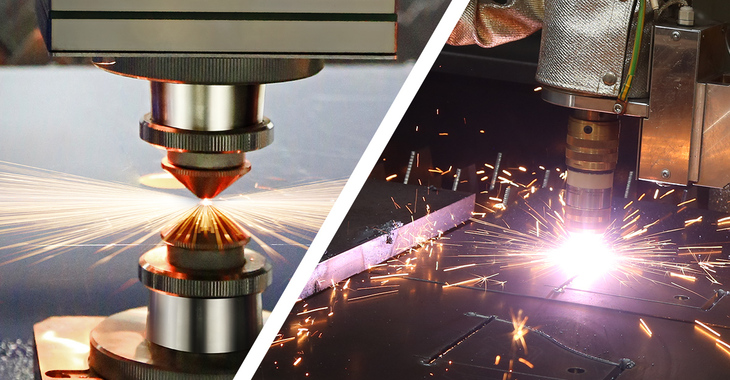
Laser or plasma - is the choice easy?
Cutting machine manufacturers talk about technology comparisons and argue that their solutions are superior to others on the market. This is natural from a marketing point of view. However, it is important to consider whether the manufacturer of a technical solution can reliably refer to other solutions on the market and, above all, whether they have sufficient knowledge to be able to make comparisons at all.
Each technology is designed for a different production profile. Cutting machine manufacturers know this best, as they offer all available technologies as well as combined technologies. The task of competent salespeople is to advise the customer on the most favorable solutions for them.
Features of laser technology
Laser cutting is the most modern method of thermal separation of materials. It is very precise and fast. Compared to plasma cutting, it is more versatile. It enables the processing of various types of steel and non-ferrous metal alloys. Its range depends on the laser source used. It can also successfully cut wood, leather and selected plastics. The latest solution, which is based on "fiber" technology, generates the beam and sends it to the cutting head via a fiber optic cable, which expands the application possibilities of cutting machines and significantly reduces operating costs. It also significantly reduces power consumption. In contrast to older technologies (e.g. with a CO2 or disk source), the fibre laser (also known as a fibre laser) is characterized by both a diode source and fibre-optic guidance of the laser beam. The wavelength of the laser obtained is ten times shorter than that of a CO2 laser, which means that a higher energy concentration is achieved and more reflective materials can be cut, which was not possible with earlier technologies. Thanks to the physical differences of the laser beam, namely the 10 times shorter wavelength and the much higher energy density, we are even able to achieve a cutting speed several times higher. The laser source used by Eckert has an efficiency of over 30 percent (wall-plug efficiency), which results in three times lower energy consumption compared to the CO2 source.
Who is the laser for?
In order to give a factual answer to this question, it is necessary to analyze your own production profile. If we cut precise elements with complex shapes and holes with small diameters and expect excellent quality and high cutting efficiency, then a fiber laser equipped with linear drives should meet our requirements. It should be noted that the qualitative cutting of some shapes, such as internal angles, loops, arcs and burrs, is not possible with plasma. The laser also has a big advantage when it comes to cutting holes, allowing us to cut a 0.1 mm diameter hole in a 1 mm thick stainless steel sheet. Plasma does not perform as well in this comparison, as the minimum diameter of a quality hole in 1 mm thick sheet metal is 6 mm. Practice shows that a fiber laser can be 6 times faster than plasma when cutting thin sheets. However, it should be noted that the laser can leave a mark on the material at large thicknesses and high cutting speeds. On the other hand, plasma cutting of thin sheets can cause bevels. The greater the thickness, the greater the bevel. With black steel, the bevel can be up to 2 degrees. With other materials, it can be larger. Thanks to their dynamics, linear drive lasers have a higher acceleration than plasmas and higher travel speeds (even over 150 m/min), which shortens the machine's approach and braking distance. This has a significant impact on cutting times. It should also be noted that the cost of parts that wear out quickly is higher with plasma cutting machines. Another important factor in choosing the right technology is the heat-affected zone, which is high in plasma cutting. A high heat input can impair the properties of the material. This is particularly important for the subsequent welding of structures that are subject to UDT acceptance.
Possibilities
When it comes to the range of materials that can be cut, it is best to rely on practical experience and look at the order portfolio of fiber laser owners. Generally speaking, it can be said that these are mainly companies that manufacture "ready-to-assemble" elements on a large scale and also provide cutting services in addition to their own production. The most interesting applications of lasers in production include the manufacture of modern control panels, the production of metal elements in the furniture industry, stainless steel tanks, the construction of expansion joints, the agricultural industry, the automotive industry and the defense industry. The main customers for plasma machines are manufacturers of welded steel structures.
Technological innovations
The technology of material processing with fiber lasers is constantly being developed and improved. The focus of development is on optimizing productivity and cutting quality. One new solution used by Eckert is magnetic linear drives. Their design is not based on moving parts, which makes these drives more reliable and enables greater positioning and repeat accuracy. The result is a stable cutting process that is as precise as possible. Greater cutting machine dynamics are achieved by increasing the acceleration and travel speed of the machine. Shorter travel times and shorter cutting times lead to lower daily operating costs. With this latest development, the cutting speed is practically only limited by the power of the power source.
Invest rationally
When choosing the right cutting technology for your production area, don't just look at the price. Remember that EU funds, although limited, are still available. They are primarily earmarked for projects that best achieve the objectives of the Europe 2020 strategy. - This means investments that are innovative, based on new technologies, environmentally friendly, etc. Companies in the start-up phase can also apply for such aid, the value of which can even reach more than half of the planned investment. At the investment planning stage, it is also worth seeking professional advice from manufacturers offering all the technologies available on the market. These companies not only have knowledge and extensive experience, but above all can offer a wide range of solutions that meet customer expectations and are optimally adapted to the specifics of production.