Preparation for joining, beveling the edges during cutting.
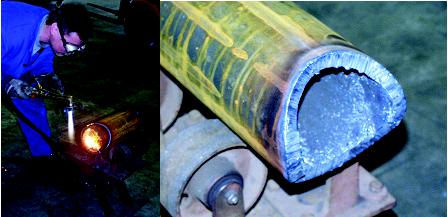
Every welder and production technologist is familiar with the problem that occurs when chamfering the edges of parts to be welded. The larger the components are (e.g. in ship and bridge building) or if the components are made of thicker materials (especially in mining and the defense industry), the greater the problem.
Even today, most factories still cut parts perpendicular to the material and then prepare the welding phases. The process is such that the perpendicular cut piece is transported to a finishing station where it is beveled with a milling machine, oxy-fuel or plasma torch. It is often also ground. This lengthens the production process, which in turn leads to higher costs.
Solutions that have recently become increasingly popular are 3D cutting machines and robots that can cut and bevel materials at any angle. In addition to shortening the production process by at least 4 times, their use guarantees further measurable benefits:
- Saving space in the hall - no bulky inclined stand is required, which emits harmful gases, dust and noise and also needs to be protected for safety;
- Lower work intensity and possibility of more optimal deployment of employees;
- No additional transport of workpieces required;
- Higher work culture in the hall due to the elimination of the noise source (grinding machine);
- Reduced fire risk due to the elimination of manual burners and gas tanks.
plasma cutting systems and oxyfuel cutting systems are the most popular due to their low cost and wide range of applications. The reason for this is obvious: structural steel with a thickness of 4 to 50 mm is most frequently used for the production of welded structures. Practical trials with 45° bevel cutting using a plasma cutter have shown that it works well with material thicknesses of 1 to 35 mm. The flame cutting machine, on the other hand, is effective up to a thickness of 200 mm.
The design of a machine for beveling sheet metal is a major challenge for manufacturers. Particular attention must be paid to the positioning of the cutting head, its rotatability and the compensation of the cutting angle deviation.
Maintaining a constant torch distance from the material is also crucial for high edge quality, especially in plasma cutting. As a rule, the material to be cut does not have an absolutely smooth surface. It is also subject to the stresses and temporary thermal influences exerted by the plasma during cutting.
In plasma cutting, the reference element for measuring the torch distance to the material is the plasma arc voltage. However, this voltage, which is easy to measure in principle, depends on many parameters. In addition to the height of the torch, the relative angle of the torch, the current intensity and the composition of the gas mixture are also important. Controlling such a complex process requires computerized motion control and adaptive height adjustment.
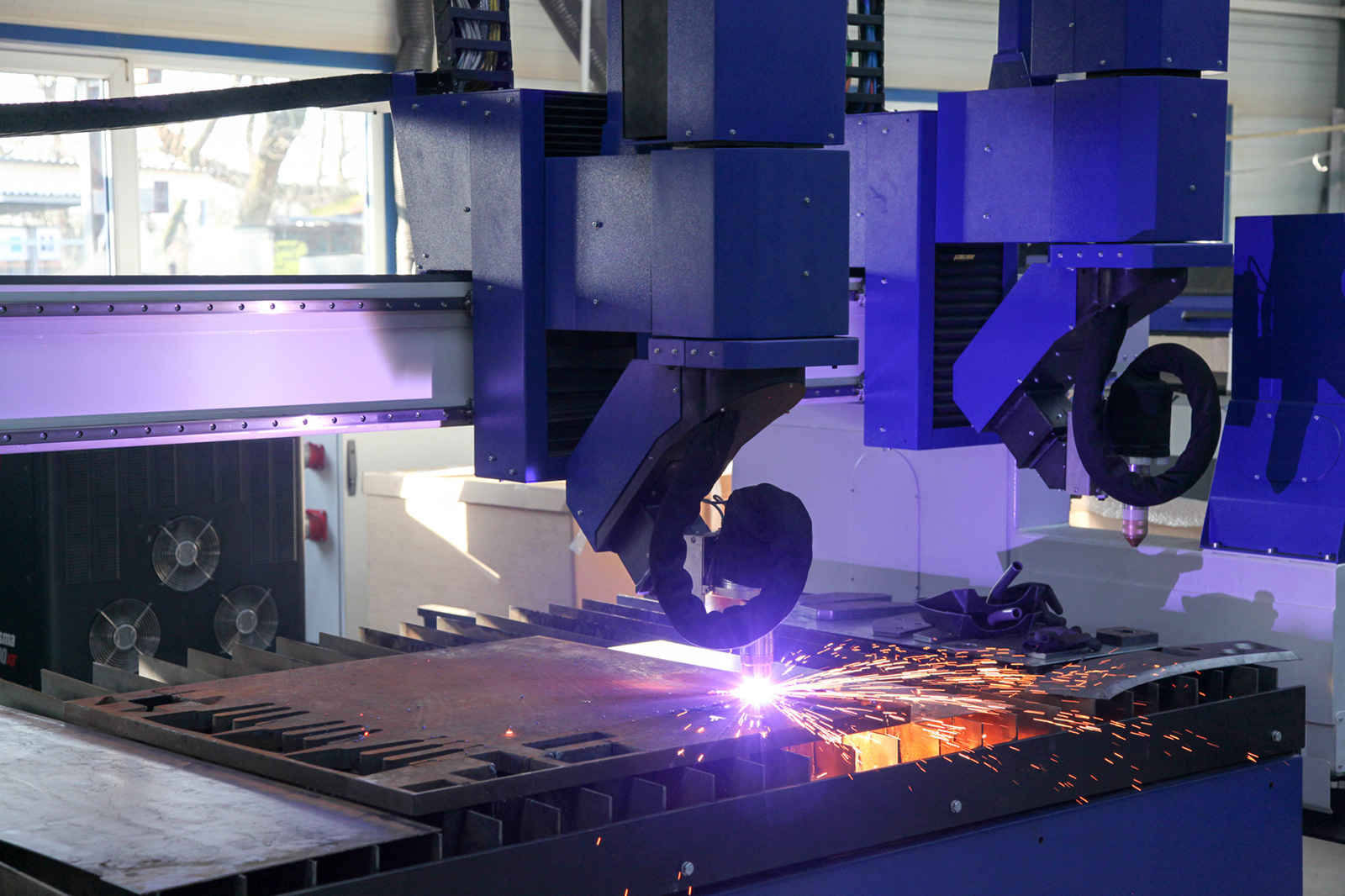
Another advantage of chamfering systems is the ability to chamfer tubes directly during cutting. Similar to sheet metal, this option significantly shortens preparation time, improves logistics and reduces costs. It is of great importance for large-scale projects such as the construction of a stadium or a bridge, where several thousand pipes with multiple connections are often used.
Special CAD software is used to design such structures. It automatically determines the required amount of material as well as the type and number of connections, thus reducing calculation time and errors to a minimum.
While cutting machines with a fixed cutting head have been in the lead until now, interest in 3D cutting machines is now growing. They offer very measurable advantages in conjunction with a reduction in costs and a shortening of the time required to produce an element. Safety issues and the improvement of work hygiene in production facilities should not be neglected either. Eckert's solution from Legnica stands out from other solutions of this type available on the market. It uses innovative technologies that enable completely flexible and efficient use of the 3D cutting functions.